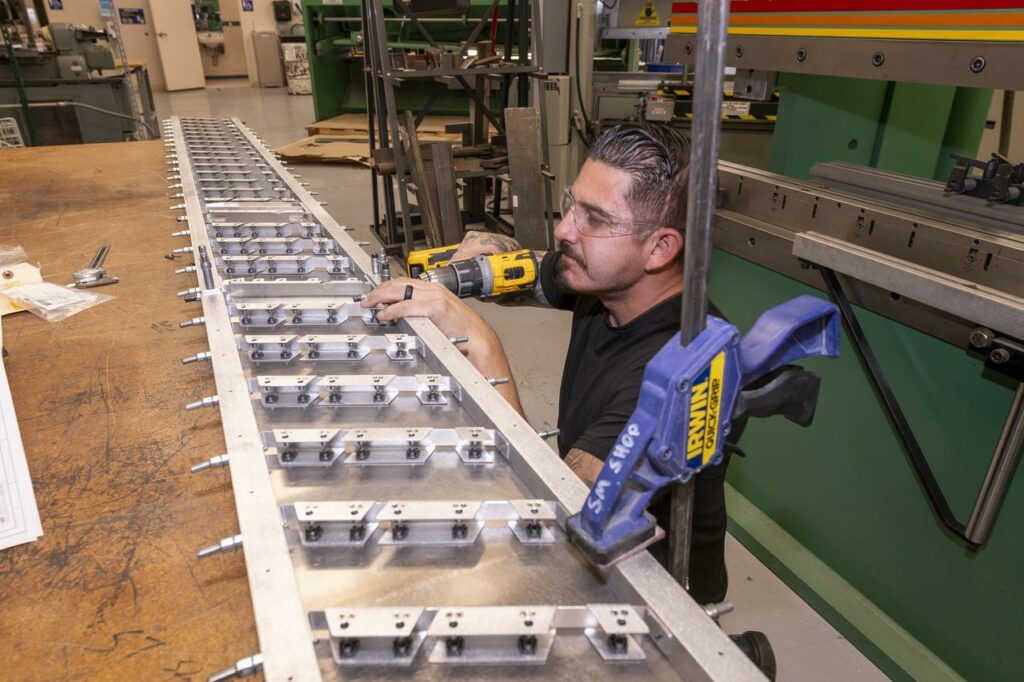
Nesta semana, compartilhando um interessante vídeo, a Administração Nacional Aeronáutica e Espacial dos Estados Unidos (NASA) informa que técnicos de sua Oficina de Fabricação Experimental criaram peças para a montagem do modelo da nova asa transônica suportada por treliça (TTBW – Transonic Truss-Braced Wing), que deverá ser utilizada pela Boeing em seus futuros aviões.
Baseados no Armstrong Flight Research Center (Centro de Pesquisa de Voo) da NASA em Edwards, Califórnia, os técnicos também montaram seções e fizeram uma verificação final para garantir que o modelo da asa estava pronto para testes.
Confira no player a seguir as imagens e, abaixo do vídeo, leia mais detalhes sobre os trabalhos que aparecem na gravação:
Entre as imagens do vídeo acima, o alemão Escobar trabalha em uma estrutura de asa modelo que possui duas laterais compridas e barras entre elas, que lembra uma mini-escada. Ele lixa as arestas, usa quatro tornos para fixá-las e usa uma fresadora que programou para fazer furos de precisão.
Escobar é um dos técnicos da Oficina de Fabricação Experimental do Armstrong Flight Research Center. A equipe fez 29 tipos diferentes de peças, mais de 50 unidades no total, para montar um modelo de asa exclusivo de 10 pés (3 metros) que ajudará a calibrar a instrumentação de fibra óptica e contribuirá com dados para um futuro modelo de asa para mostrar como o projeto melhora a eficiência de consumo de combustível.
O modelo de asa experimental possui muitos recursos do X-66, como foi denominado o avião que a NASA utilizará para os testes da TTBW. A asa do X-66 vai ser fixada na aeronave usando suportes diagonais que também geram sustentação e podem resultar em uma aerodinâmica significativamente melhorada.
Os muitos recursos do NASA Armstrong permitiram o projeto, a fabricação e o teste do início ao fim do modelo de asa. O Laboratório de Cargas de Voo forneceu especificações para o modelo, incluindo alguns de seus próprios cálculos de um teste de asa eficiente de 6 pés (1,8 metro) realizado em 21 de dezembro de 2022. O projeto de Tecnologia Avançada de Transporte Aéreo da NASA financiou as asas do modelo.
Além disso, o Armstrong e o Centro de Pesquisa Langley da NASA em Hampton, Virgínia, estão trabalhando em uma proposta para uma asa de 15 pés (4,6 metros) chamada Experimento Estrutural de Asa Avaliando Suporte por Treliças (Structural Wing Experiment Evaluating Truss-Bracing). Essa asa incluiria testes de vibração do solo que dariam uma imagem mais clara de como reagiria a diferentes tipos de vibração durante o voo.
Andrew Holguin, engenheiro de design, criou representações 3D das peças e de como montá-las. Ele dividiu o trabalho do modelo em sub-montagens para facilitar o foco em um único conjunto de tarefas. Com o projeto totalmente aprovado e as ordens de tarefa redigidas, Escobar iniciou seu trabalho.
Segundo explica a NASA, a capacidade de trabalhar itens simultaneamente é uma vantagem. Jose Vasquez, um técnico de engenharia, usou um software para instruir uma fresadora de cinco eixos sobre como cortar, girar e transformar um bloco de aço em um adaptador. A água jorra no mecanismo de corte para evitar que tudo fique muito quente.
Assim que a peça foi finalizada, Vasquez a removeu da máquina, limpou-a e usou um par de paquímetros e uma ferramenta de medição fina, chamada micrômetro, para verificar se o adaptador atende às necessidades precisas do modelo da asa. Se não existir uma ferramenta de calibração para verificar um componente especializado, os técnicos poderão fabricá-la.
Em outra parte do laboratório, o técnico em chapas metálicas Matt Sanchez usou uma prensa dobradeira para fazer dobras em uma folha de alumínio, para formar um retângulo chamado nervura de asa. Em outra etapa, ele adicionou mais peças às nervuras e posteriormente instalou-as na asa modelo.
Com a montagem quase concluída, foi providenciada a cobertura externa da asa. Sanchez montou os desenhos, colocou uma folha de alumínio na mesa de jato de água e iniciou o trabalho com a serra até o corte completo.
Para encerrar esta parte do trabalho, ele fez uma verificação bem-sucedida de todos os componentes, chamada verificação de ajuste.
Com o modelo da asa concluído, a equipe do Laboratório de Cargas de Voo continua concluindo o projeto e os preparativos para construir um dispositivo para os testes da asa. O acessório se juntará ao modelo experimental de asa, testará a instrumentação e permitirá testes que podem contribuir para a próxima inovação na aviação.