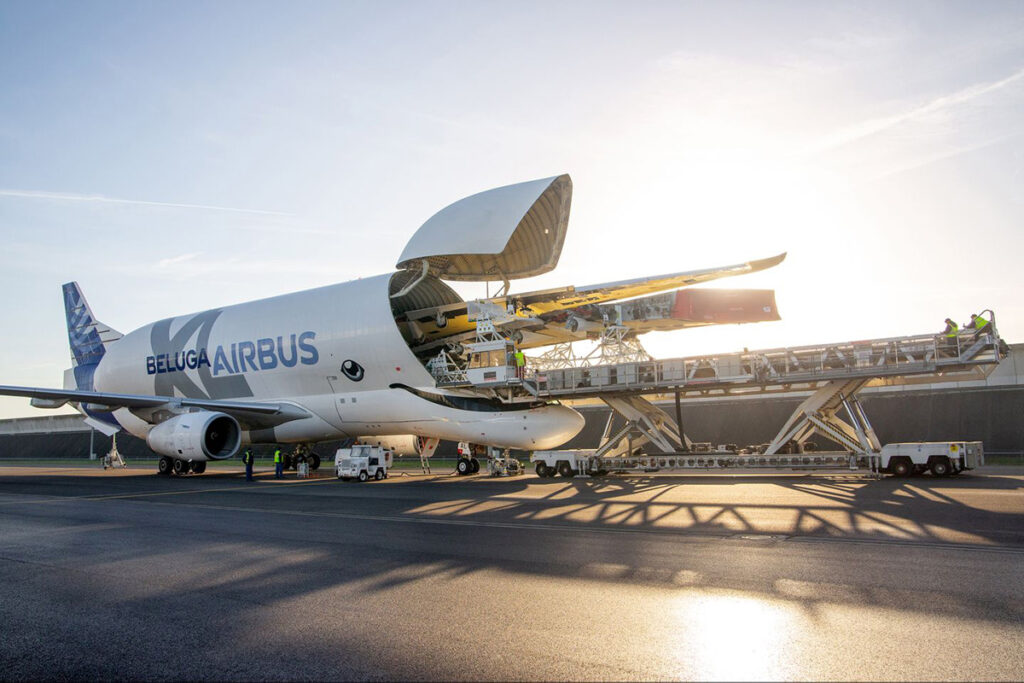
No último episódio de uma série de explicações sobre o desempenho das aeronaves da Airbus, bem como suas curiosidades, foi explorada a fabricação e o funcionamento das asas.
Nesse âmbito, o programa de pesquisa “Wing of Tomorrow” está empenhado em examinar as tecnologias e sistemas industriais que poderiam impulsionar uma nova aeronave com baixa emissão de carbono aos céus. Antes de adentrar nos avanços futuros, é crucial compreender como as asas são produzidas atualmente.
São os trabalhadores de montagem da Airbus que unem as asas às fuselagens. E eles são impactados a cada momento. Hoje, por exemplo, cerca de 100 novas tecnologias estão sendo exploradas para auxiliá-los e promover avanços no design e na fabricação das asas. E o “Wing of Tomorrow” representa o maior projeto de pesquisa em curso, sendo o epicentro dessas inovações.
O objetivo do programa é desenvolver abordagens disruptivas, capazes de viabilizar novas aeronaves com baixa emissão de carbono. Algumas dessas inovações podem até ser aplicáveis às plataformas de aeronaves atuais da Airbus. E isso é importante para a fabricante, que acredita que, antes de vislumbrar o futuro, é importante compreender o presente.
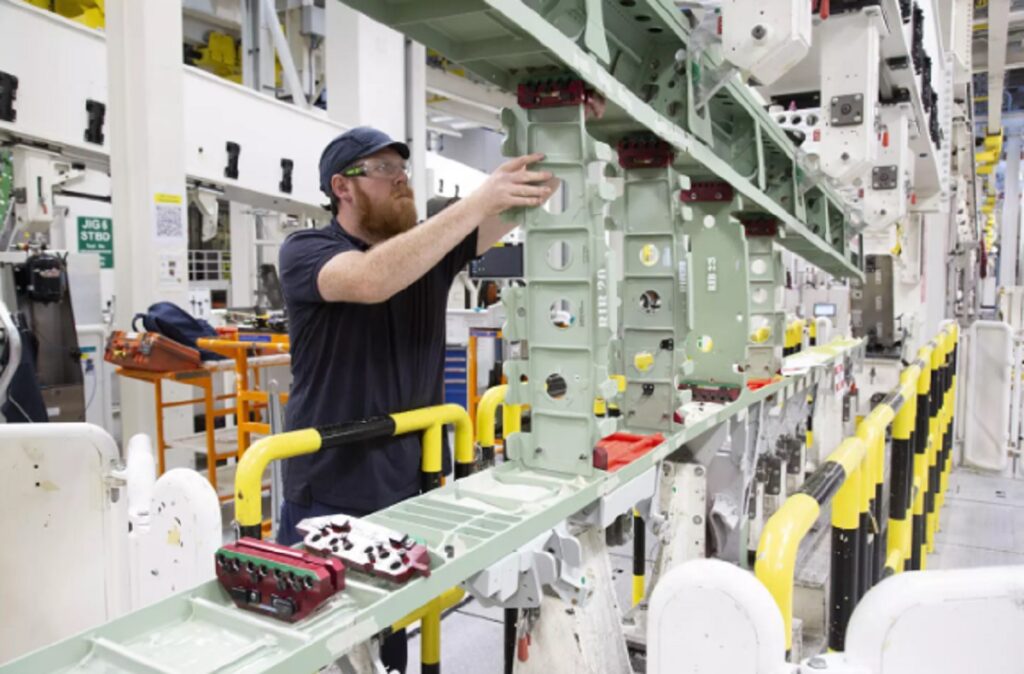
Montando o quebra-cabeça
O processo de montagem das asas na Airbus assemelha-se à montagem de um quebra-cabeça complexo.
Tome-se como exemplo o A350. Assim como em todos os programas de aeronaves comerciais da Airbus, os materiais compostos das asas e outros componentes, como longarinas e nervuras, são fabricados em múltiplos locais distintos e distantes entre si. Posteriormente, os operadores realizam a montagem das asas na fábrica em Broughton, no Reino Unido.
Cada conjunto de asas do A350 finalizado é transportado pelo BelugaXL, um avião de transporte, operando com uma mistura de 50% de Combustível Sustentável de Aviação (SAF), até Toulouse. Lá, são unidas a caixa central da asa e a fuselagem, durante a montagem final.
Antes que esse quebra-cabeça de produção possa ser concluído, há muito a ser feito. O processo inicia-se na fase de Projeto Geral da Aeronave, que determina a forma e as características da asa, incluindo controles de voo e sistemas de elevação. Posteriormente, inicia-se uma fase denominada “co-design“, na qual o design estrutural da asa é amadurecido em paralelo com o sistema industrial necessário para produzi-la.
Mais longa, fino e leve
Olhando para o futuro, prevê-se que as asas sejam produzidas com níveis mais elevados de automação. Utilizando um processo denominado “design para fabricação”, os engenheiros da Airbus identificarão o melhor equilíbrio entre montagem manual e automatizada, assegurando que as asas sejam produzidas corretamente da primeira vez, a cada vez e a um custo adequado.
A próxima geração de asas será caracterizada por sua maior extensão, maior leveza e perfil mais esguio. Quando combinados, esses atributos contribuem para que uma aeronave alcance a sustentação necessária consumindo menos combustível, resultando em menores emissões de CO₂.
Essa transformação no design das asas requer uma adaptação na forma como são produzidas. O sistema industrial da Airbus precisa estar preparado para produzir de maneira eficiente uma asa tão leve em volume e ritmo. Essa mudança exige uma reavaliação radical e é nesse ponto que entra o “Wing of Tomorrow”.
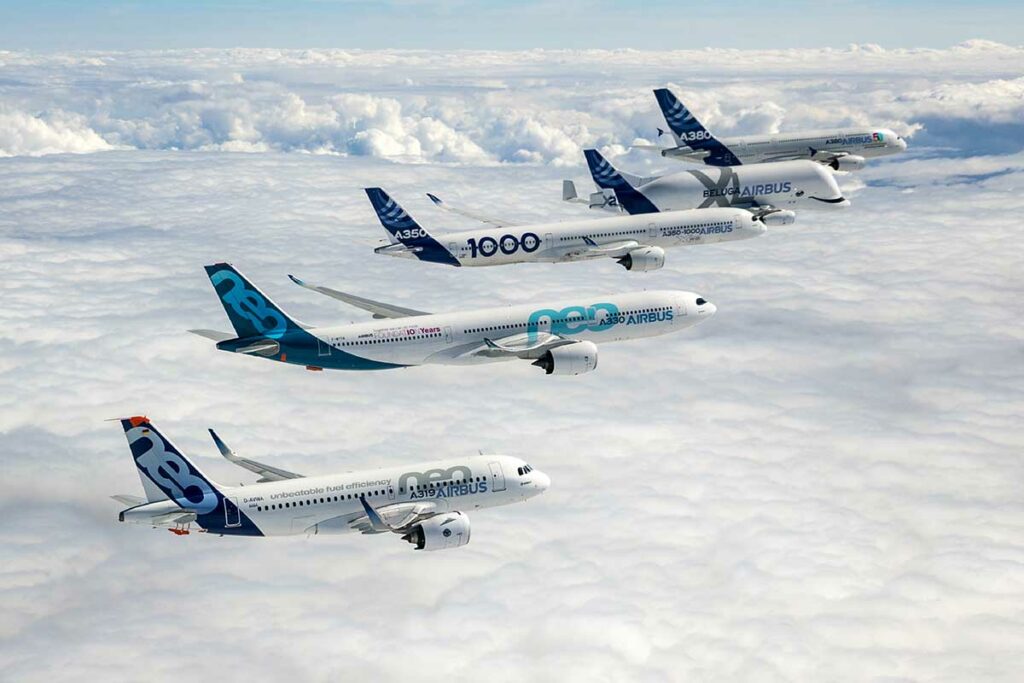
Seu propósito é não apenas preparar as tecnologias necessárias para a próxima geração de aeronaves, mas também capacitar os funcionários, a cadeia de suprimentos, o sistema industrial e a capacidade física e digital da empresa. Todos trabalharão em conjunto para proporcionar a agilidade necessária para expandir a produção em velocidade, levando em consideração o impacto sobre os operadores que fabricam as asas diariamente.
Ciclos de produção mais curtos
O “Wing of Tomorrow” está conduzindo a Airbus a uma nova era de capacidade industrial, servindo como um campo de testes para novas técnicas de manufatura e automação que unem eficiência e melhorias ergonômicas. Por exemplo, a produção poderá ver a introdução de linhas de montagem de produtos múltiplos, semelhantes às encontradas em instalações automotivas.
Isso permitiria que a Airbus trabalhasse em diversas partes da asa simultaneamente, possibilitando ciclos de produção mais curtos e montagem mais rápida. A automação de perfuração, por exemplo, não apenas reduz os prazos, mas libera operadores qualificados para tarefas de maior valor agregado.
Além disso, a Airbus está utilizando modelagem digital para orientar o design das futuras fábricas de asas, otimizando o tempo de produção. Esse modelo digital de operações, conhecido como “gêmeo digital”, auxilia a Airbus a avaliar o impacto de cada processo de montagem em termos do uso mais eficiente de materiais, redução de resíduos e emissões de carbono.
Florescer das demonstrações
Montados no Advanced Manufacturing Research Centre (AMRC) em Broughton, Reino Unido, três demonstradores de asa em tamanho real serão usados para avaliar diferentes aspectos da construção de asas da próxima geração.
Os demonstradores são todos feitos de compósitos leves e produzidos em colaboração com 40 parceiros em todo o mundo, com o objetivo geral de identificar quaisquer gargalos que possam impedir que as tecnologias que apresentam sejam utilizadas em futuras gerações de aeronaves.
Os três demonstradores em tamanho real são:
Demonstrador de asa estática – usado para testar as capacidades estruturais de novos designs e materiais;
Demonstrador totalmente equipado – usado para testar tecnologias de instalação e novas abordagens para equipar a próxima geração de asas com sistemas;
Demonstrador Run@rate – usado para testar a capacidade industrial e as tecnologias de automação da Airbus para avaliar como construir asas em escala e ritmo.